Northwest Rubber Extruders is committed to consistently meeting or exceeding our customers’ requirements for products and services. We ensure quality every step of the way by implementing quality management processes for everything from document and record control, to manufacturing and shipping. We also hold three industry certifications for the manufacturing of extruded and molded products for a range of industries including aerospace and automotive.
Our quality control laboratory is staffed and equipped for complete quality conformance testing along with research and development to support our customers’ needs. As recommended by the American Society of Automotive Engineers (SAE), we utilize the American Standard Test Methods (ASTM) for quality testing of all our extrusions and molded products. Additional testing resources are available upon request.
Learn more about our quality control processes and standards by reading about our testing capabilities and viewing our quality policy. If you have additional questions, please contact us for more information.
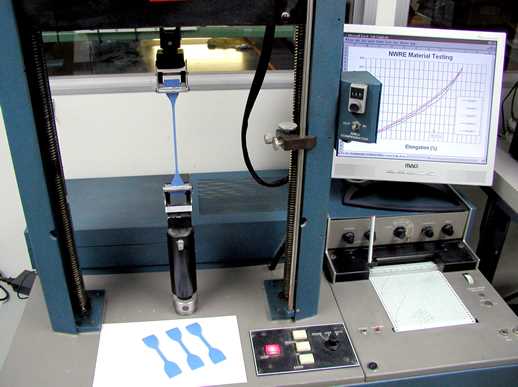
Quality Certifications
Quality is more than a statement; it’s the way we execute every project from order placement to final product delivery. Northwest Rubber Extruders is registered to ISO9001, AS9100 and IATF 16949 standards to help ensure our customers receive quality service and products.
ISO 9001 Certification
ISO 9001 is a certification that specifies the requirements for a quality management system, including a company’s ability to provide customers with products that consistently meet statutory and regulatory requirements. ISO 9001 certified companies also strive to enhance customer satisfaction by continuously improving quality management processes and ensuring the processes meet statutory and regulatory requirements.
View our ISO 9001 Certificate of Approval for the manufacture of custom extruded and molded organic, silicone and thermoplastic elastomeric products.
AS 9100 Certification
The AS 9100 certification includes quality management system requirements for aerospace organizations that design, develop and/or produce products for the aerospace industry. This certification is based on the Society of Automotive Engineers (SAE) quality management requirements and addresses requirements for process approach, regulatory requirements for products and services, and the implementation of processes for continued improvement.
View our AS 9100 Certificate of Approval for the manufacture of custom extruded and molded organic and silicone products for the aerospace industry.
IATF 16949 Certification
IATF 16949 s a technical specification for the development of quality management systems and regulations for the automotive industry. The certification outlines best practices for increasing customer satisfaction and using preventative measures to ensure quality management during the manufacture of customer-specified parts.
View our IATF 16949 Certificate of Approval for the manufacture of custom extruded and molded organic, silicone and thermoplastic elastomeric products.
Customer Focused Quality Assurance Policy
Our quality management team is customer focused and committed to enhancing customer satisfaction by ensuring all customer requirements are determined, implemented, and communicated throughout the organization. We measure product conformity and on-time delivery performance on a regular basis and use our metrics to make improvements as needed.
At Northwest Rubber Extruders, it’s our mission to exceed customer expectations by providing unsurpassed customer service with quality parts at cost-effective prices. As part of our quality assurance policy, we identified our core processes, support processes, sub-processes and outsourced processes, as well as how information flows to and from our customers.
Quality Assurance Process
The scope of our quality management system is the manufacture of custom extruded and molded organic, silicone and thermoplastic elastomeric products in compliance with ISO/TS 16949, ISO9001 and AS9100 quality standards.
Our core process review covers every step of the purchasing, manufacturing and shipping process to ensure we meet each customer’s requirements and satisfaction. We also perform quality management for all support processes, including the timely review and revision of all company documents and identification and storing of quality records.
The key areas of our quality assurance policy include:
- Management Commitment: for the development and implementation of the quality management system and continuous improvement of its effectiveness.
- Resource Management: for allocating adequate resources and personnel with the education, trained skills, and experience to ensure that verification activities can be handled in a thorough and effective manner.
- Product Realization: to ensure that all production activities are planned and defined before initiating the order and are carried out under controlled conditions.
- Measurement, Analysis & Improvement: to ensure conformity and continual improvement of the effectiveness of the quality management system.
For an in-depth look at our quality processes, view the full version of our Quality Assurance Policy Manual.
Delivering Quality Products and Services
Our goal is to deliver high quality extrusions, moldings and other rubber products that exceed your expectations. All products are manufactured in compliance with industry standards and we offer quality conformance testing in our laboratory.
Contact Northwest Rubber Extruders for additional product and process information or request a quote.